Energy Efficient Hot Water Boiler Plant Design Series
Featured
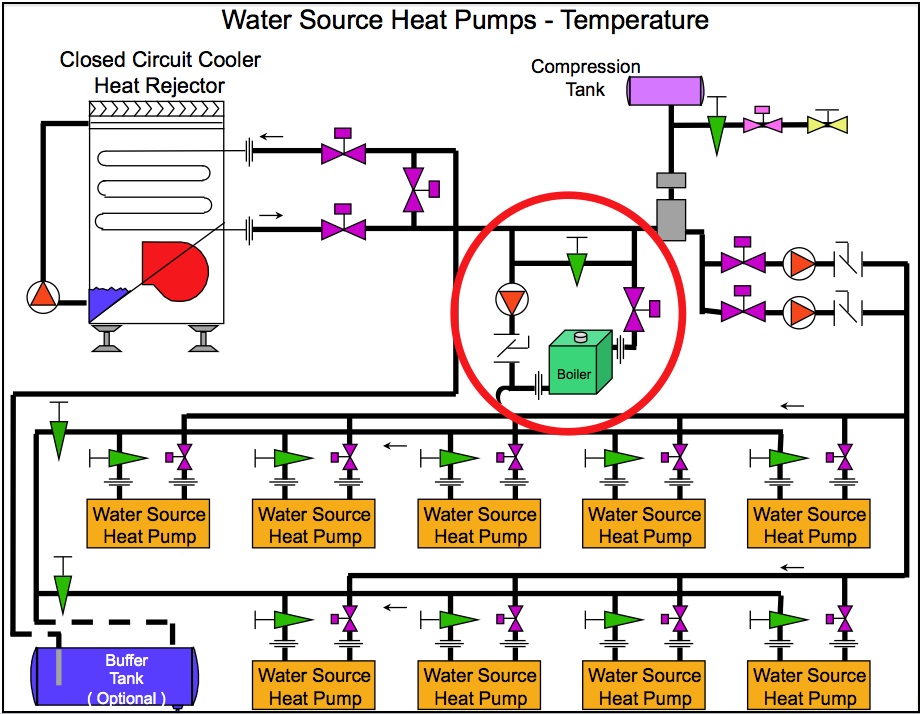
Energy Efficient Hot Water Boiler Plant Design Part 6: Best Applications for Condensing Boilers
Condensing boiler applications dovetail nicely with most of today’s energy efficient HVAC strategies, as well as ASHRAE 90.1 – 2010 and 2013 requirements. New and existing boiler plants are ripe with opportunities for condensing technology and can offer payback in as little as 2-3 years. Here we’ve listed some of the top applications for condensing boilers and why they are a good choice in each situation...
So you’ve decided to use condensing boilers on your next project – GREAT! Just remember that this decision will impact other aspects of your mechanical design. Condensing boilers DO NOT operate properly in systems that are designed around traditional non-condensing technology.
A properly applied condensing boiler generates a lot of condensate – 5 gallons for every 1,000,000 BTUH input. In a large commercial or institutional building this can easily add up to several hundred gallons per week. But where does all that condensate go?
Condensing boilers have made a strong case for themselves in terms of both space and energy efficiency. Of course, the latter hinges on one critical factor: the condensing boiler must condense. And if condensation is intended as an ongoing occurrence, the correct materials and equipment must be specified to withstand the harsh effects of condensation.
Condensing boilers now dominate the new construction and replacement commercial markets. Here at JMP we estimate that as much as 90% of new boilers we sell are condensing boilers. So how did we get here and what is it about the technology that transformed the marketplace?
It takes approximately 1000 Btus of energy to convert one pound of water into vapor. Think of that as the price you pay as part of the combustion process in a typical non-condensing hydronic boiler. That’s a good starting place for this next series on Energy Efficient Hot Water Boiler Plant Design.